Passivation
- Home
- Passivation
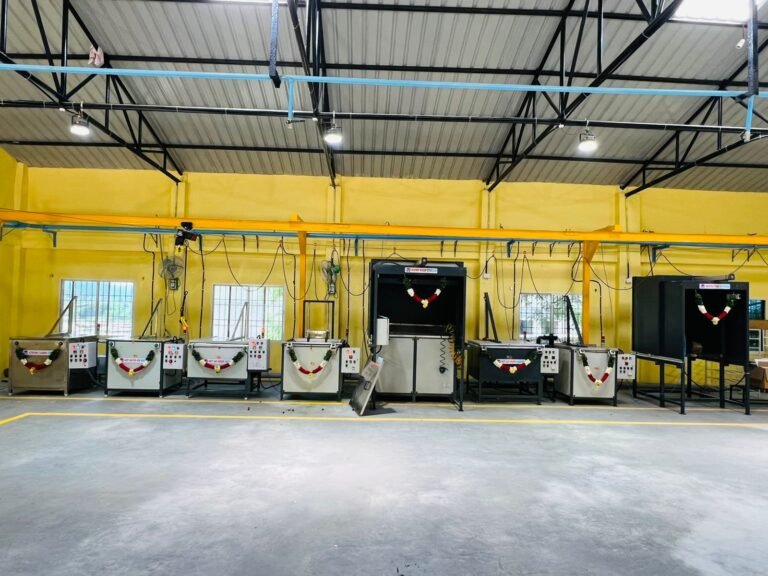
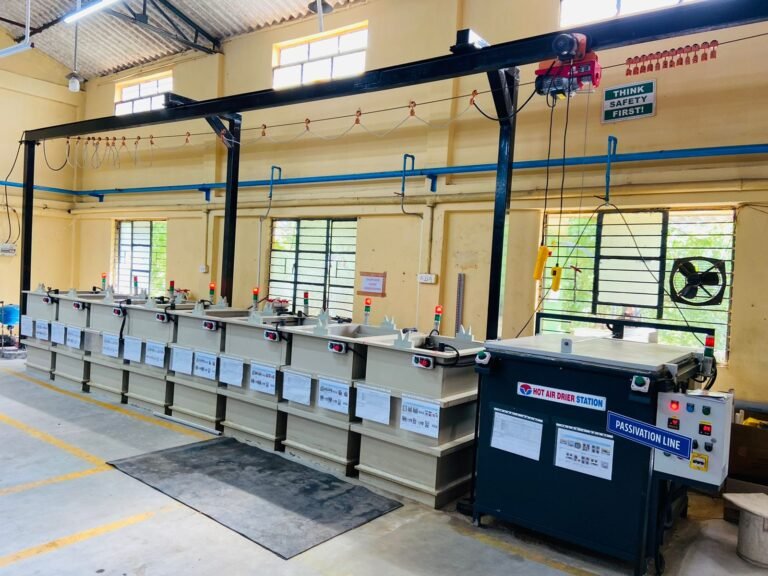
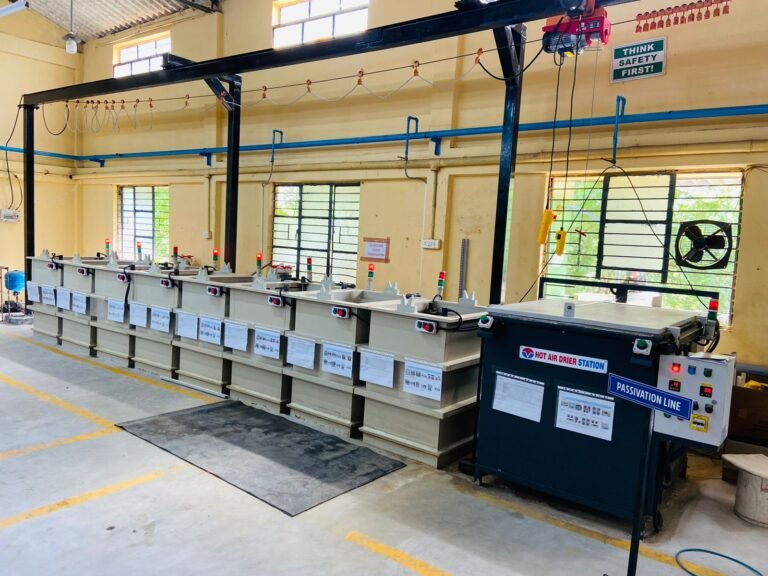
Passivation
Passivation treatment given to corrosion resisting and heat resisting steels to enhance corrosion resistance, after manufacturing processes such as machining, roll forming, die shaping etc., The Process covers the requirements for a process to assure removal of free iron or other less noble contaminants from the surface of corrosion resistant steel parts.
Standard Reference
ASTM-A967 – Chemical Passivation Treatments for Stainless Steel Parts / Components
Methods
Passivation method as per Nitric – 4 (The solution contains 45 to 55 volume percent of Nitric acid. The parts shall be immersed for a minimum of 30 Min at a temperature in the range from 49° to 54°)
Applicability
- The process consists of subjecting the items to a solution that removes surface contaminants that may accelerate corrosion and reforms the surface oxide film upon which the corrosion resistance of the material largely depends.
- The process used typically to dissolve loose metallic elements from the surfaces of corrosion resistant steels to improve their corrosion resistance.
- Passivation shall be carried out as late in the manufacturing sequence as possible, after all manufacturing operations such as machining, forming, welding, heat treatment, blasting, chemical etching and pickling have been completed.
- Blasting and pickling or etching solutions that remove metal, scale and oxide, will also remove the oxide film that Passivation produces.
- This process is applicable to austenitic and non-austenitic corrosion resistant steel.
Testing Method
- The testing method is as per ASTM A967 Standard practice D Copper sulfate test.
- The examination shall be reported in Passivation Test report (VE/F/37)